Cost Accounting
Ending Inventory: Calculation, Definition
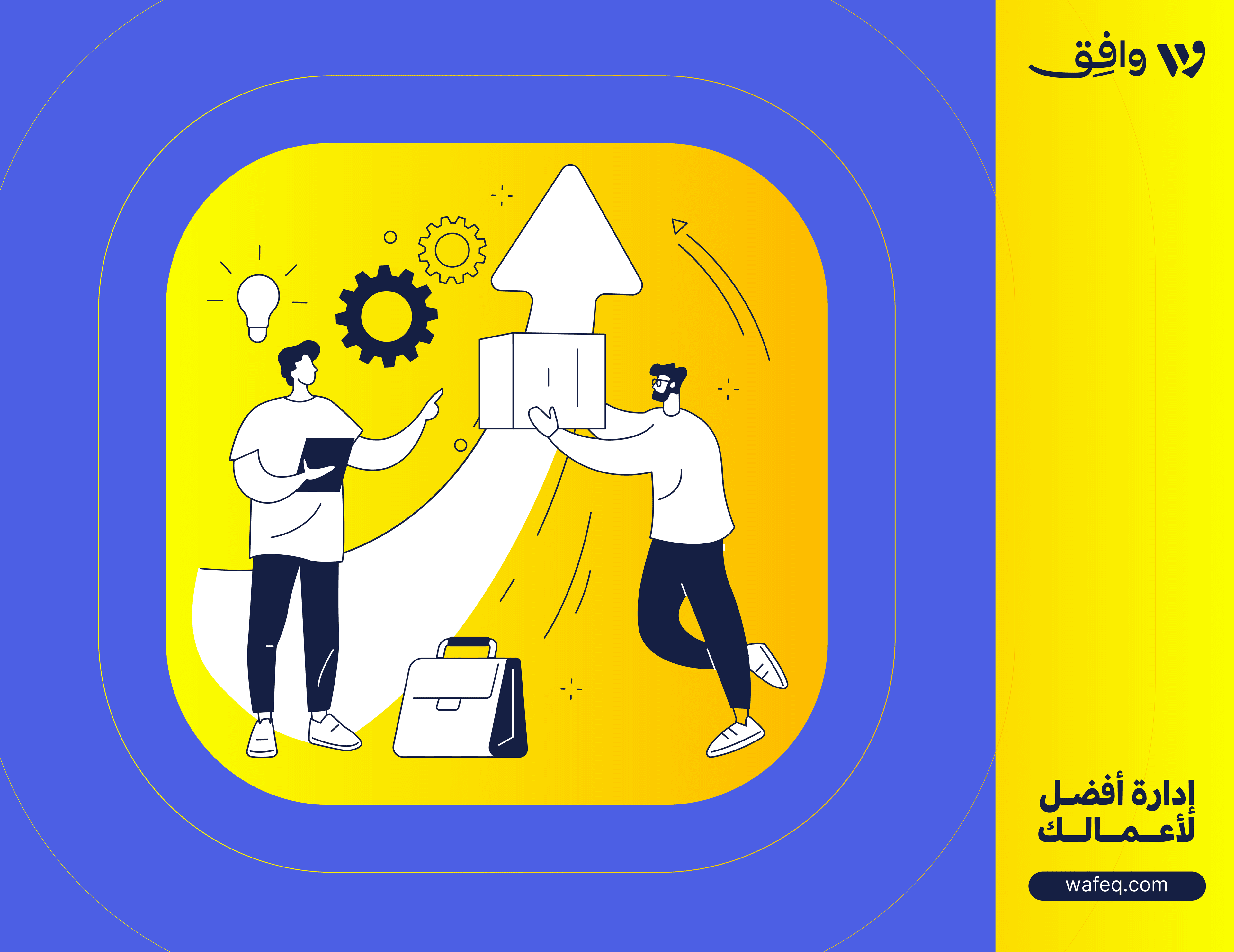
To know what a company profited, the ending inventory needs to be calculated most of the time. This might sound simple, but often, it is more complex than it seems, so getting all the details right is essential—read on to find out everything you need to know about the matter.
How Does Ending Inventory Work?
The value of products in stock and held by a corporation at the end of an accounting period is known as ending inventory. There are several valuation techniques that may be used to determine the ending inventory valuation.
The management-selected inventory valuation technique has an impact on the value of ending inventory, even when the actual number of units in the ending inventory matches across all methods.
Main Takeaways
- Ending inventory has a significant role in determining a company’s cost of goods sold (COGS).
- The technique selected to put a monetary value on COGS and inventory has an influence on the balance sheet and income statement values.
- The three most popular approaches for valuing ending inventory are weighted-average cost (WAC), last-in, first-out (LIFO), and first-in, first-out (FIFO).
Ending Inventory Simply Explained
The simplest way to determine ending inventory is to add new purchases to the beginning inventory and then deduct the cost of products sold (COGS).
Note: A physical inventory count can produce a more precise ending inventory. However, this is frequently impractical for bigger enterprises.
The difficulty of inventory counts may be made easier by improvements in inventory management software, RFID systems, and other technologies utilizing linked devices and platforms.
A major asset on the balance sheet is ending inventory. It's crucial to appropriately disclose closing inventories, especially when applying for financing. As part of a debt covenant, financial institutions frequently demand that certain financial ratios, such as debt-to-assets or debt-to-earnings ratios, be maintained by the date of audited financials.
Investors and creditors actively watch audited financial accounts for firms with high inventories, such as retail and manufacturing.
Read in detail about Inventory Valuation.
In addition to terminating inventory under normal business conditions, inventory may also need to be written off for a number of reasons, such as theft, drops in market value, and general obsolescence. If there is a significant decline in customer demand for the goods, inventory market value can go down.
Similarly to this, if a newer version of the same product is introduced while the stock of the previous version is still present, obsolescence may result. This kind of circumstance would be most typical in the rapidly evolving technology sector.
Auditors may demand that businesses confirm the precise amount of inventory they actually hold on hand.
A physical inventory count is beneficial because it enables businesses to compare what is really in stock with what their computer systems have recorded at the conclusion of an accounting period.
Any mismatch between an organization's real ending inventory and what is reported in its automated system may be the result of shrinkage, which is the loss of inventory due to a variety of factors, such as theft, vendor or accounting errors, delivery issues, or any other relevant problem.
Important Considerations
Three distinct categories of materials are included in the phrase ending inventory. Materials that are ready to be produced into finished items are referred to as raw materials and are employed in the initial production process.
The second term, "work-in-process," describes materials that are being transformed into finished things. Finished goods are the name given to the last category. These products have completed the manufacturing process and are now prepared for customer purchase.
Numerous common financial statement KPIs are impacted by the technique of inventory value that management chooses. Cost of goods sold, gross profit, and net income are all components on the income statement that relate to inventory. The balance sheet is where current assets, working capital, total assets, and equity are found. These are all crucial elements of the financial ratios that are used to evaluate the performance and health of a company's finances.
Last In, First Out (LIFO)
One of the three widely used techniques for assigning costs to the ending inventory and cost of goods sold (COGS) is last in, first out (LIFO).
It is based on the supposition that the things the business most recently bought were utilized in the creation of the products that were sold first throughout the accounting period.
In other words, it is predicated on the idea that the most recent orders would be fulfilled first.
The cost of the most recent purchases is initially allocated to COGS under LIFO, while the cost of older purchases is assigned to ending inventory—which is still in stock at the end of the period.
First In, First Out (FIFO)
FIFO makes the assumption that the company's oldest purchases were utilized to create the products that were sold first. Simply put, this technique implies that the first products ordered will be the first to be sold.
When using FIFO, the cost of the most recent purchases is added to the ending inventory, which is still available at the end of the period, while the cost of the oldest purchases is added to COGS first.
Weighted Average Cost (WAC)
The weighted average cost approach divides the total cost of goods bought or produced in a period by the total number of things bought or produced to get the cost of ending inventory and COGS.
It "weighs" the average since it accounts for the volume of goods bought at various price points.
The Conclusion
As we can see, ending inventory is of utmost importance for most firms out there. Calculating it is not only vital for the COGS of a corporation but can also drastically influence the major financial statements of a firm. Choosing the right method is also essential, as there can be key differences between the results of each calculation type.
Start with Wafeq
Use Wafeq to keep all inventory and goods on track to run your business better.